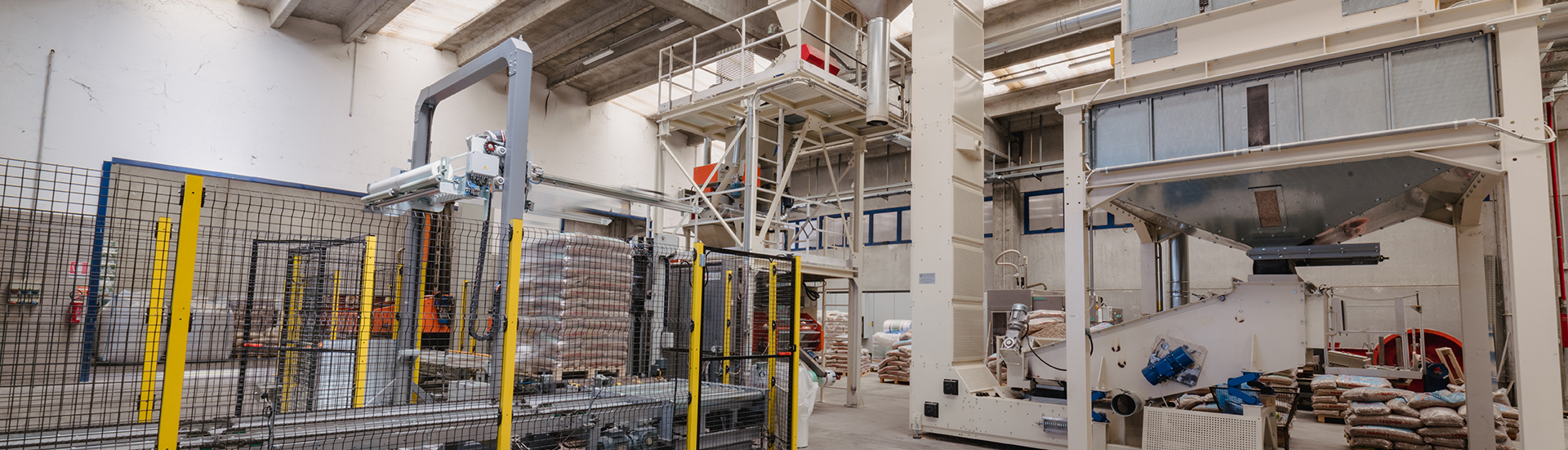
PELLET PLANTS
Our systems are highly technological PLANTS for PELLET production of different materials, such as wood, alfalfa (lucerne), industrial waste, MSW – RDF and more, and our solutions can be “TURN-KEY”, starting from a productivity of 1000 kg/h up to large quantities according to the different customer needs and the specific environmental requirements.
EHW systems are characterized by cutting-edge technology, with very high performances and low maintenance, as well as low energy consumption.
In line with the concept of 4.0 industry, EHW plants are equipped with a system of remote control and assistance, with the possibility of transmission and storage of the historical data packages, as well as the monitoring and the automatic adjustment of the main operating parameters, designed to ensure optimal process conditions.
EHW ITALIA is specialized in the supply of CUSTOM MADE TURNKEY PELLET PLANTS, according to the customer’s needs.
Depending on the raw material available, we will proceed with the study of the project choosing the machinery necessary for the pellet plant, starting from the preparation of the material and the relative crushing process by means of a hammer mill, going then on with the drying of the processed material through our single or multiple deck belt dryers, granulation by pellet press, the cooling of the material, and finally the transfer to the packaging department according to the chosen package solution.
Crushing
Our hammer mills, equipped with sturdy frames, are ideal for the reduction and grinding of the raw material, both wet and dry, in order to reach an ideal dimension of particle size. After grinding, the material is forwarded to the next step of the pellet plant to be dried and pelletised.
Drying
Given an ideal moisture content of pelletising material of about 12%, it will be necessary to use a dryer for the desiccation of wood or material from wetter biomass.
Pellettisation
Our pellet mills can be supplied with capacities starting from 1 ton/h up to 10 ton/h for large pellet plants.
Cooling process
Once the pelletising process is completed, the temperature of the product is between 60 and 80°C and a cooler is needed to reduce it. After the cooling process, pellet will be transferred to the packaging department.
Our plants are characterized by cutting-edge technology, with very high performances, low emissions and reduced energy consumption
RAW MATERIAL LOADING LINE
divided in two boxes From the first box the WET SAWDUST loading line starts, directly flowing into the dryer loading bunker, while the WOOD CHIPS loading line starts from the second box, which is equipped with a roughing mill to pre-grind the wood chips and make THE DRYING PROCESS easier.
DOUBLE WET / DRY MATERIAL LOADING LINE
with the loading of the dry material downstream of the dryer, automatically dosed
LOADING SYSTEMS FOR BIG SIZES
composed of various boxes to automatically mix the various types of wood, wood chips and sawdust
YOU WANT TO KNOW MORE ABOUT OUR PLANTS FOR THE PRODUCTION OF PELLETS AND DRYERS?
Get in touch with us by leaving your contacts on the form below and we will be at your service in a short time to provide you with all the support you need.